- Product display
- CNC CORNER FORMING MACHINE
- Lateral Punching Machine
- ALUMINUM PLATE SHARP CORNER FORMING MACHINE
- Laser Welding Platform
- CNC HYDRAULIC LOWER TRANSMISSION BENDING MACHINE
- CNC BUSBAR PROCESSING MACHINE
CNC Corner Forming Machine TOP-FA·DML3780
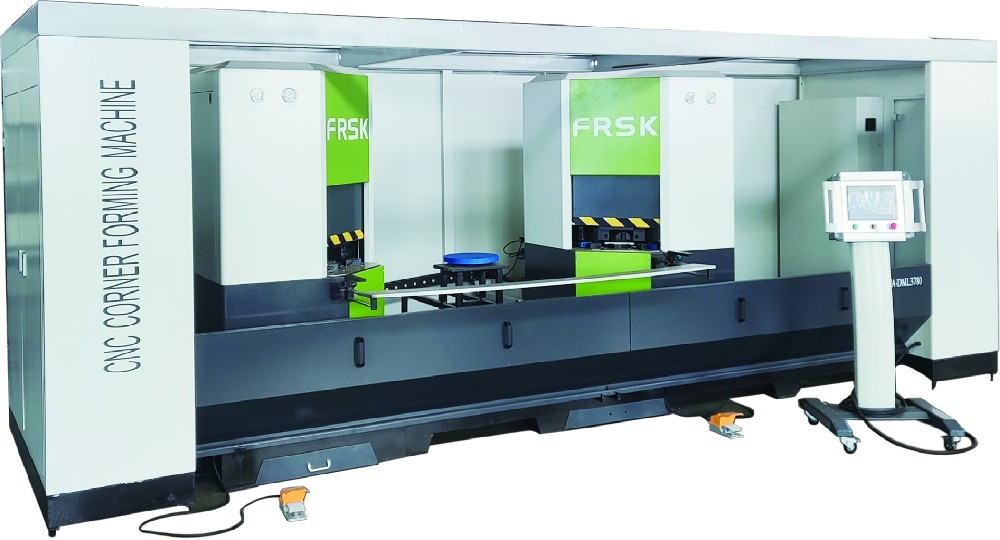
Application Area
■This model is used in cold-rolled plate ,aluminum plate,galvanized plate etc double corner simultaneous forming, Widely used in the switching door ,cover plate ,aluminum single panel curtain wall , switchboard ,container cover, household appliances ,instruments and other fields.
Technical Features
■This model owns double corner simultaneous forming function ,when the door panel size is in the range:780mm-2800mm ,servo motor controls the door panel size.worker or robot puts the door panel in the forming moulds ,mechanical arm positions the door panel automatically ,two machines starts to work at same time and turns into rolling and stretching state ,after machine returns ,put the others two corners in the mould ,the machine starts to finish double corner simultaneous forming,only two steps the door panel can be finished ,it will take about 40 secs to process one door panel,It will faster 20 secs than single machine ,greatly improve the production efficiency .
■when door panel size is less than 780mm ,this model can be changed to two single machines,two workers can process door panel corner forming seperately ,it is very convinient and flexible .flange height of the workpiece can be flexible and varied ,when the flange height is changed ,just exchange the forming inner mould you can achieve the ideal height .when the machine processes 304 or higher level stainless steel plate ,due to the material characteristics,shear knife wears quickly and will be changed in time ,this model is the most advanced machine in the world.
Technical parameter | Content | |||
Model | TOP-FA·DML3780 | |||
Processing range (mm) | Material | Thickness | Flange height(mm) | Coner radius |
Cold-rolled plate | 0.6 | <10 | 1.5-30 | |
0.8-1.2 | <20 | 1.5-30 | ||
Cold-rolled plate | 1.5 | <25 | 1.5-30 | |
2.0-3.0 | <30 | 1.5-30 | ||
Aluminum plate | 1-3 | Same as the flange height of cold rolled plate | 1.5-30 | |
Processing time moulding one corne | About 7 sec. | |||
Processing length range | 780mm-2800mm | |||
Processing time moulding fours corners | About 32 sec | |||
Mould configuration | Rolling mould ,square mould ,shear knife | |||
Main motor power(KW) | 8 | |||
Dimensions(Length×Width×height) (mm) | 5860*1820*2230 | |||
Weight(KGS) | 5350 |
Standard Model: TOP-FA·DML3780 ,processing range: 780mm-1900mm
CNC Corner Forming Machine TOP-FA·D3150
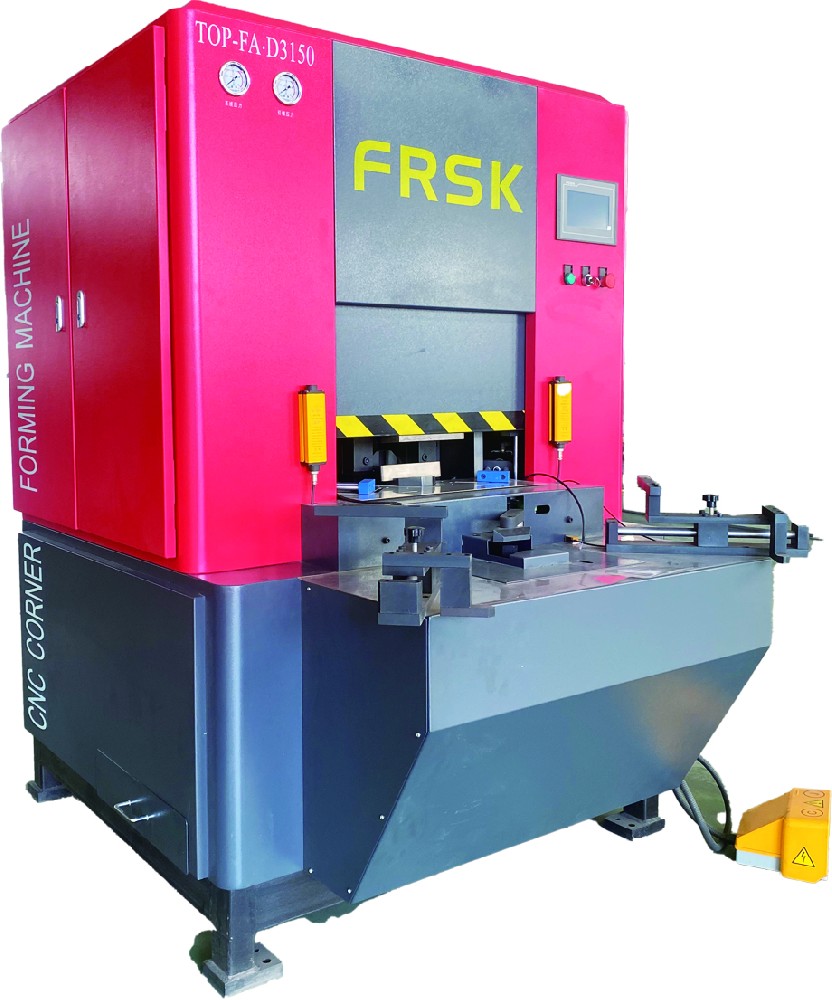
Application Area
■This machine is used in the processing of sheet metal corner moulding such as cold-rolled plate ,aluminum plate ,stainless steel plate ,copper plate etc.
■Widely used in the switching door ,cover plate ,aluminum single panel curtain wall , switchboard ,container cover, household appliances ,instruments and apparatus.Laboratory platform.safe box and other fields
Technical Features
■This model owns mechanical arm automatic positioning workpiece device ,changes the previous method of manually pulling workpiece to make the workpiece symmetric ,improve forming effect .It is convinient for the robot to connect with the machine achieving automatic production,improve production efficiency ,reduce labor cost .
■This model owns two shear knives ,inner shear knife and external shear knife which is on the operation platform .Inner shear knife is suitable for the workpiece of big size and fixed flange height ,reduce replacement frequency and save labor.External shear knife is suitable to process stainless steel products,big corner radius workpiece.TOP-FA.D3150 and FA-NC3150 these two models own same corner forming effect .
■There are four forming methods you can choose :
(1).Put the bent plate on the forming triangle inner mould then pull tightly by hand,step on the contour foot swich, the rolling mould comes down to the bottom position to finish corner mouldng , moulding process is finished all parts return .
(2)ManualAuto:click “ManualAuto”to red ,pull the plate tightly by hand corner moulding will be finished automatically ,no need to step on the contour foot switch.
(3).InductionAuto: click“InductionAuto” to red,the corner moulding will be finished automatically once put the plate on the square mould ,no need to step on the contour foot switch.
(4).FootAuto:click”FootAuto”to red ,after put the plate on the square mould,step on the foot switch the corner moulding will be finished automatically .
technical parameters | Content | |||
Model | TOP-FA·D3150 | |||
Processing Range (mm) | Material | Thickness | Flange height (mm) | Corner radius |
Cold-rolled plate | 0.6 | <10 | 1.5-50 | |
Cold-rolled plate | 0.8-1.2 | <20 | 1.5-50 | |
Cold-rolled plate | 1.5 | <25 | 1.5-50 | |
Cold-rolled plate | 2.0-3.0 | <30 | 1.5-50 | |
304(higher level included)Stainless steel plate | 0.5-2.5 | 1-2mm lower than the flange height of the cold rolled plate | 1.5-50 | |
Aluminum plate | 1-3 | Same as the flange height of cold rolled plate | 1.5-50 | |
Processing time moulding one corner | About 7 sec. | |||
Processing time moulding fours corners | About 32 sec. | |||
Mould configuration | Rolling mould ,square mould ,shear knife | |||
AC servo motor | Fuji/Japan | |||
Pneumatic System | Airtac/Taiwan | |||
PLC | FATEK/Taiwan | |||
Low voltage electrical appliance | Schneider/France | |||
hydraulic valve | Huade/China | |||
Main motor power(KW) | 4 | |||
Dimensions(Length×Width×height) (mm) | 1700*1370*1970 | |||
Weight(KGS) | 1650 |
CNC Corner Forming Machine FA-NC3150
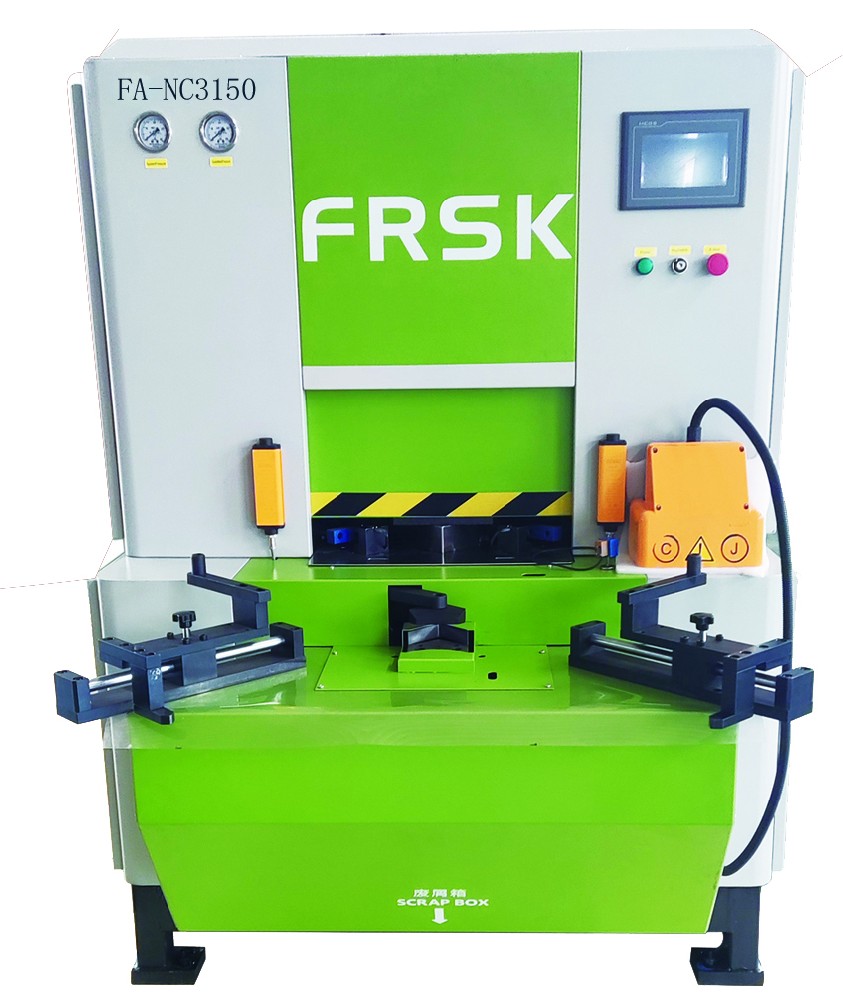
Application Area
Technical Features
■This model owns mechanical arm automatic positioning workpiece device ,changes the previous method of manually pulling workpiece to make the workpiece symmetric ,improve forming effect .It is convinient for the robot to connect with the machine achieving automatic production,improve production efficiency ,reduce labor cost .
1.Suitable for processing door panel products such as high and low voltage electrical cabinets, air-source heat pump covers, file cabinets, explosion-proof electrical appliances, air conditioning external units etc.
2.Changing the traditional process of open-angle welding ,grinding etc into rolling ,stretching and forming directly by the CNC corner forming machine , Stretch leftover material will be sheared by platform shear knife.The workpiece doesn’t need to be welded and grinded , solve the problems of manual welding,grinding , high labor costs,difficult recruitment , also solves the problem that the welded corner will rust in a long time .The processed products by the CNC corner forming machine is beautiful ,the quality will improve to a high level .
3.Flange height of the workpiece can be flexible and varied within the stretching range ,the plate can be processed within machine range,such as cold-rolled plate,304 stainless steel plate ,aluminum plate ,copper plate etc. Install safety light curtain protection to make the production process more safe and humanistic .
■There are four forming methods you can choose :
(1).Put the bent plate on the forming triangle inner mould then pull tightly by hand,step on the contour foot swtich, the rolling mould comes down to the bottom position to finish corner mouldng , moulding process is finished all parts return .
(2)ManualAuto:click “ManualAuto”to red ,pull the plate tightly by hand corner moulding will be finished automatically ,no need to step on the contour foot switch.
(3).InductionAuto: click“InductionAuto” to red,the corner moulding will be finished automatically once put the plate on the square mould ,no need to step on the contour foot switch.
(4).FootAuto:click”FootAuto”to red ,after put the plate on the square mould,step on the foot switch the corner moulding will be finished automatically .
technical parameters | Content | |||
Model | FA-NC3150 | |||
Processing Range (mm) | Material | Thickness | Flange height (mm) | Corner radius |
Cold-rolled plate | 0.6 | <10 | 1.5-50 | |
Cold-rolled plate | 0.8-1.2 | <20 | 1.5-50 | |
Cold-rolled plate | 1.5 | <25 | 1.5-50 | |
Cold-rolled plate | 2.0-3.0 | <30 | 1.5-50 | |
304(higher level included)Stainless steel plate | 0.5-2.5 | 1-2mm lower than the flange height of the cold rolled plate | 1.5-50 | |
Aluminum plate | 1-3 | Same as the flange height of cold rolled plate | 1.5-50 | |
Processing time moulding one corner | About 9 sec. | |||
Processing time moulding fours corners | About 60 sec. | |||
Mould configuration | Rolling mould ,square mould ,shear knife | |||
AC servo motor | Fuji/Japan | |||
Pneumatic System | Airtac/Taiwan | |||
PLC | FATEK/Taiwan | |||
Low voltage electrical appliance | Schneider/France | |||
hydraulic valve | Huade/China | |||
Main motor power(KW) | 4 | |||
Dimensions(Length×Width×height) (mm) | 1720*1330*1770 | |||
Weight(KGS) | 1360 |
CNC Corner Forming Machine E3150
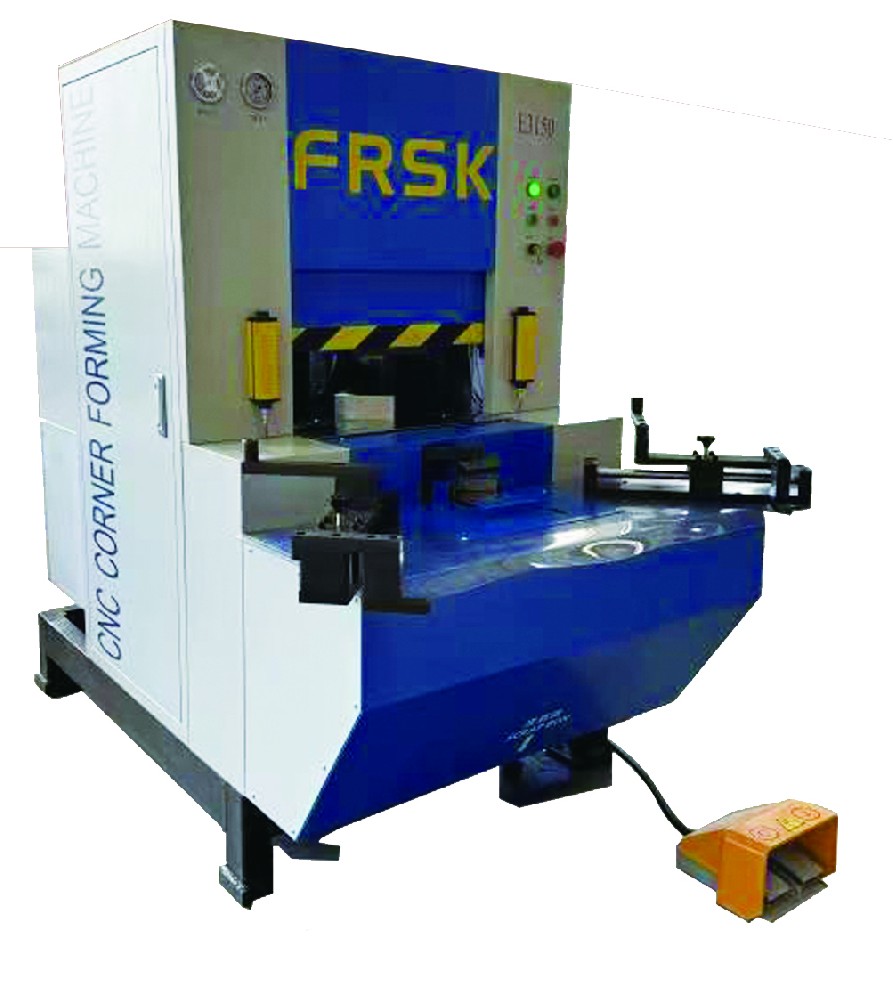
Application Area
Technical Features
■This model is economical type ,operator puts the door panel on the forming mould ,pulls door panel gently towards your body ,then the squeeze board will reset the door panel automatically ,rolling mould will do stretching movement ,after corner forming finished,operator changes position to shear the stretched superfluous wastes.if thickness is changed ,operator needs to use
tools to adjust the clearance to necessary position ,then the machine can process in mass production ,good forming effect .this corner-wrapping machine is highly appraised by customers.
technical parameters | Content | |||
Model | E3150 | |||
Processing Range (mm) | Material | Thickness | Flange height (mm) | Corner radius |
Cold-rolled plate | 0.6 | <10 | 1.5-50 | |
Cold-rolled plate | 0.8-1.2 | <20 | 1.5-50 | |
Cold-rolled plate | 1.5 | <25 | 1.5-50 | |
Cold-rolled plate | 2.0-3.0 | <30 | 1.5-50 | |
304(higher level included)Stainless steel plate | 0.5-2.5 | 1-2mm lower than the flange height of the cold rolled plate | 1.5-50 | |
Aluminum plate | 1-3 | Same as the flange height of cold rolled plate | 1.5-50 | |
Processing time moulding one corner | About 9 sec. | |||
Processing time moulding fours corners | About 60 sec. | |||
Mould configuration | Rolling mould ,square mould ,shear knife | |||
Pneumatic System | Airtac/Taiwan | |||
PLC | FATEK/Taiwan | |||
Low voltage electrical appliance | Schneider/France | |||
hydraulic valve | Huade/China | |||
Main motor power(KW) | 4 | |||
Dimensions(Length×Width×height) (mm) | 1600*970*1600 | |||
Weight(KGS) | 1255 |
Lateral Punching Machine PHL-15

Application Area
Technical Features
Lateral punching machine is supporting machine for CNC corner forming machine ,solving customers’ problem of punching holes on the side . If there are fixed screw holes near the corner ,the holes will be deformed after work piece is finished corner forming in the CNC corner forming machine .Lateral punching machine is your best choice for solving side punching to avoid deformation of corner holes
Aluminum Plate Sharp Corner Forming Machine
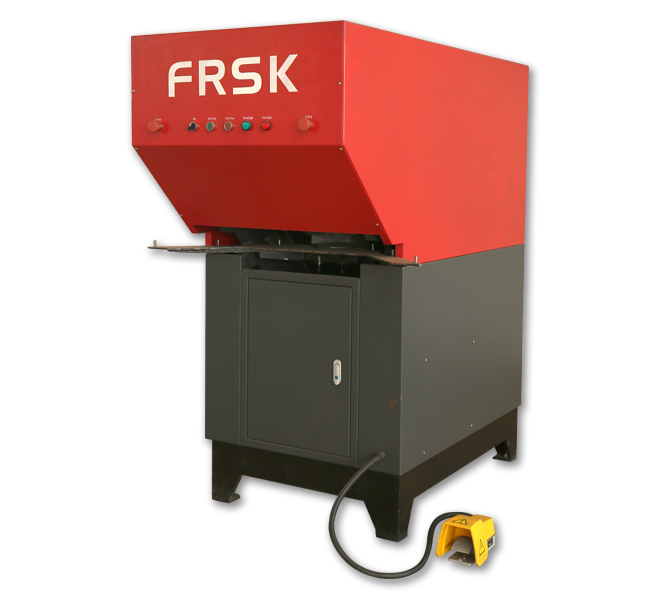
Application Area
■ It is the special equipment designed for technical standard of aluminum plate industry.
■It is suitable for four 90°corners of the interior panel in the aluminum single panel curtain wall ,no seam between the spliced corners .
Technical Features
■Aluminum plate sharp corner forming machine used together with the cnc corner forming machine ,makes the aluminum plate production faster,four shape corners are beautiful and consistent ,the quality are steady and realiable .
■The aluminum plate is produced without grinding ,welding ,estimates the tedious process of open-angle ,welding ,grinding etc.
Use methods:
1.bend the four sides of the aluminum plate in the bending machine , reserve the corners
2.four corners are initially formed in the cnc corner forming machine
3.four corners of the aluminum plate are shaped in the sharp corner forming machine separately .
4.cut the superfluous flash
Model | LDB—J—50 Aluminum plate sharp corner forming machine |
Plate thickness(mm) | 0.8mm--3.0mm |
Plate dimension(mm) | 150*150 Max no limited |
Dimension(L*W*H)(mm) | 1300*900*1650 |
Laser Welding Platform
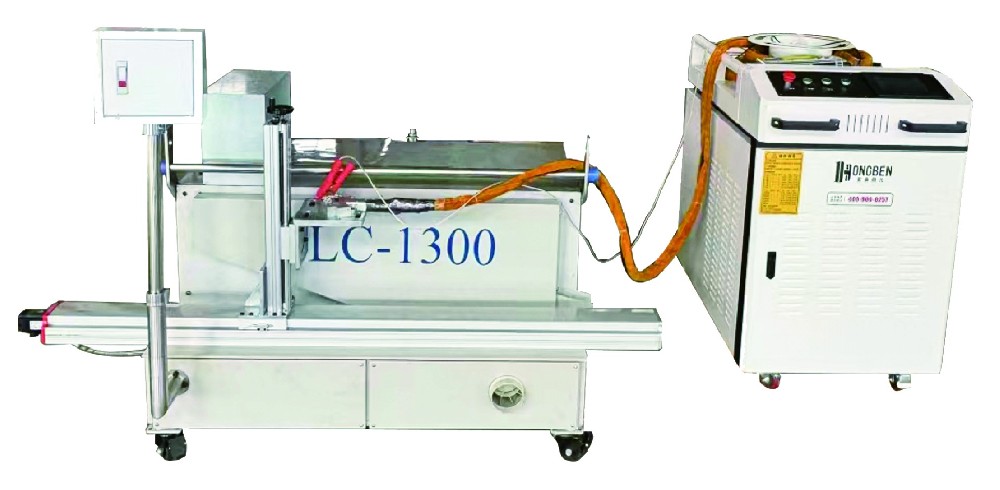
Application Area
Technical Features
Model | LC-1300 |
Laser type | Continuous fiber laser |
Peak power output | 1500W |
Controlling power range | 10%-100% |
Laser center wavelength | 1060-1080nm |
Output Mode | Continuous/Modulating |
MAX.modulation frequency | 50kHz |
Power instability | <3% |
Optical fiber output interface | QBH |
Indicating system | Red light |
Fiber length | 10m |
Welding gun type | galvanometer welding head swing from side to side |
Collmating focal length | 60mm |
Focal length | 150mm |
Wire feeding diameter | 0.8、1.0、1.2、1.6 |
Welding gun weight | 0.7KG |
Shielding gas mode | Coaxial protection |
Weld width adjustable range | 0-6mm |
Operating ambient temperature | 10-40℃ |
Operating ambient humidity | <70% |
Operating voltage | 380V/220V |
CNC Hydraulic Lower Transmission Bending Machine
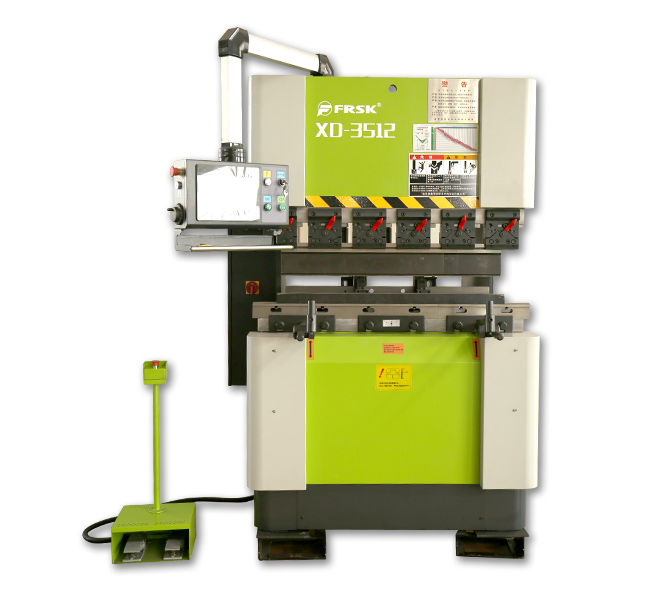
Application Area
Technical specification
XD-3512
XD-6020
XD-1030
Technical Features
1、The working speed is fast,there is no liquid filling pause when switching fast and slow,and there is no pressure relief and pressure starting process in the return journey.One travel time is short and the working speed is fast.The working speed is increased by about 50% compared with the existing lower-type bending machine
2、Programming is very simple ,no need for plate thickness,plate width,upper die,lower die,material tensile strength and other programming parameters ,the angle is directly adjusted by hand wheel.The worker can master in 5 minutes .Upload programming is at least 2 hours.
3、Low maintenance costs,no proportional valve,not affected to wear and tear,the failure rate is very low.Energy saving and consumption reduction :when working,it can save electricity and reduce consumption ,saving more than 50% of electricity compared with the existing lower bending machine .
4.To control Y axis fluctuation position at discretion by using grating.
5.speed stepless regulation:according to the work requirements,the speed can ba arbitrarily adjusted range of 10%-150%,can more effectively complete the batch processing production tasks.
6.The control system adopts the professional numerical control system NC9 or NC10,with a touch-type wire-controlled steering wheel ,and the electronic handwheel controls fine-tuning the upper and lower die-to-line and the back-end material fine-tuning .
7.It is euipped with a special bending lower die for corner forming machine and the forming effect is very good .
Technical specification | Unit | XD-3512 | XD-6020 | XD-1030 | |
Nominal pressure | kN | 350 | 600 | 1000 | |
Length of table | mm | 1200 | 2020 | 3000 | |
Distance between housings | mm | 1000 | 1700 | 2550 | |
Throat | mm | 200-250 | 400 | 400 | |
Stroke of working table | mm | 100-103 | 100-103 | 100-103 | |
Max. open height | mm | 430-435 | 430-435 | 430-435 | |
max. die setting height | mm | 310-315 | 310-315 | 310-315 | |
Speed of lower working table | approaching | mm/s | 37-47 | 52-65 | 37-47 |
bending | 7.5-1.0 | 7.0-8.5 | 7.5-9.2 | ||
returning | 47-55 | 52 | 47-66 | ||
Number of hydro-cylinder | 个 | 1 | 3 | 3 | |
main motor | kW | 3 | 5.5 | 7.5 | |
Machine precision | Slide repeating | mm | ≤±0.01 | ≤±0.01 | ≤±0.01 |
Slide positioning | mm | ≤±0.02 | ≤±0.02 | ≤±0.02 | |
Back gauge repeat positioning | mm | ≤±0.02 | ≤±0.02 | ≤±0.02 | |
Working precision | Work straightness | mm | 0.15/m | 0.15/m | 0.15/m |
Bending angle error | ′ | <±15 | <±15 | <±15 | |
Net weight | kg | 1900 | 3500 | 6500 | |
(L*W*H)Overall dimension | mm | 1320*1300*2170 | 2100×1580×2240 | 3410×1560×2560 | |
Hydraulic tank capacity | L | 33.0 | 51.0 | 70.0 |
4+2 Superposition-style Turret Busbar Processing Machine
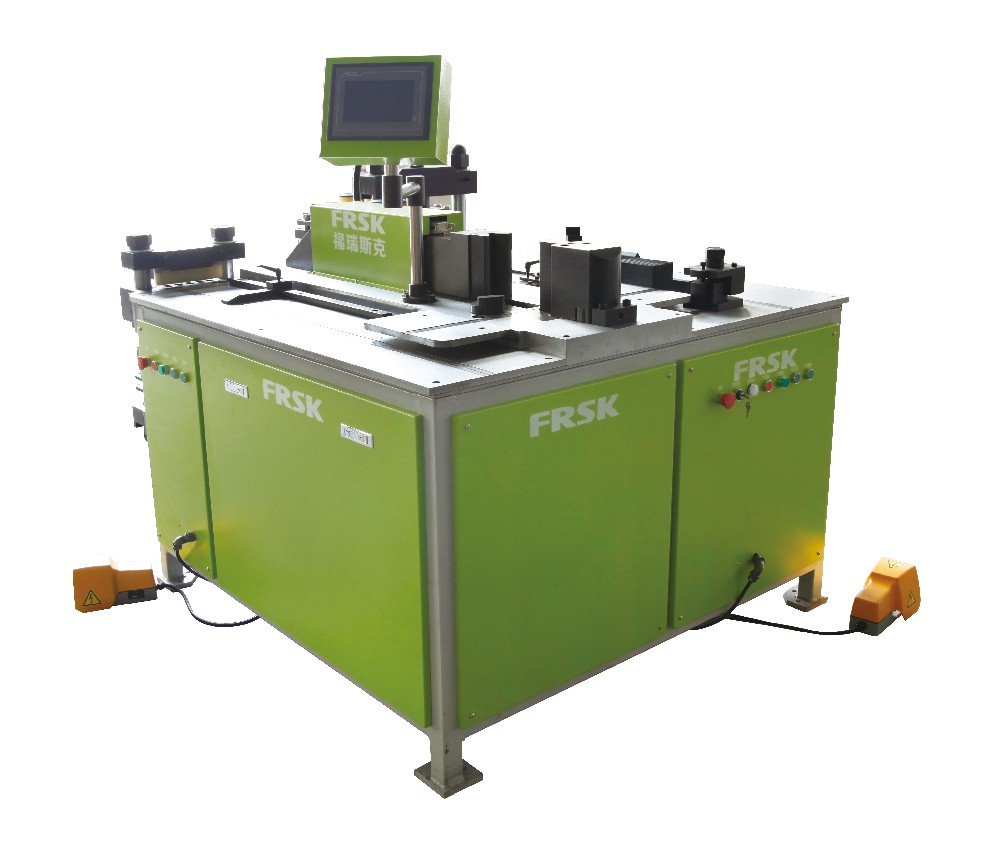
Application Area
4+2 Superposition-style Turret Busbar Processing Machine
Technical Features
1.The punching unit structure (4+2) is the best combination of four single-hole and two four- hole, large and small turntables are superposition-style and interactive,six sets of dies can be shared ,no need to be changed .When single hole needs to be punched, just manually change the angle of the single hole die, draw the punching position line of the copper bar, and then punch after fix a position with the electric light, which is convenient and fast.
2.Advantage of four-hole punching is to maximize work efficiency and reduce the labor intensity of workers ,When punching, the copper/aluminum bar does not need to move horizontally. The high-quality die base structure ensures the accuracy of punching, greatly reduces the loss of the die, and realizes the latest breakthrough in punching processing.
3.The front supporting material and the back pressing material shear at same time ,shearing workpiece double section is vertical ,no waste material .
4.copper/aluminum bar bending process is controlled by PLC and grating ruler,angle can be controlled and easy to choose ,high accurancy and efficiency .
Model/Specificaiton | 903DZTSK | 903DZTSK-2 | 903DZTSK-3 | 903DZTSK2 | 903DZTSK2-2 | 903DZTSK2-3 | |
Number of punching mode | Single hole punches four mode ,four holes punch two mode | ||||||
Punching process | Max.punching force(KN) | 900 | 900 | 900 | 900 | 900 | 900 |
Punching range(mm) | φ4.3~φ25 | φ4.3~φ25 | φ4.3~φ25 | φ9~φ21 | φ9~φ21 | φ9~φ21 | |
Max.processing thickness(mm) | 16 | 16 | 16 | 12 | 12 | 12 | |
Max.processing width(mm) | 160 | 160 | 160 | 120 | 120 | 120 | |
Shearing process | Max.shearing force (KN) | 500 | 500 | 500 | 500 | 500 | 500 |
Max.shearing thickness(mm) | 16 | 16 | 16 | 16 | 16 | 16 | |
Max.shearing width(mm) | 160 | 160 | 160 | 160 | 160 | 160 | |
Bending process | Max.bending force(KN) | 300 | 300 | 300 | 300 | 300 | 300 |
Max.bending thickness(mm) | 16 | 16 | 16 | 16 | 16 | 16 | |
Max.bending width(mm) | 160 | 160 | 160 | 160 | 160 | 160 | |
Vertical bending process | Bending width(mm) | 30~120 | 30~120 | 30~120 | 30~120 | 30~120 | 30~120 |
U-sharped bending process | Bending range (mm) | >80 | >80 | >80 | >80 | >80 | >80 |
Worktable size(mm) | 1400×1400×900 | ||||||
Main motor power(KW) | 5.5 | 5.5+4 | 5.5+2×4 | 5.5+2×4 | 5.5+2×4 | 5.5+2×4 | |
Weight(T) | 1.4 | 1.5 | 1.6 | 1.4 | 1.5 | 1.6 | |
Instruction | Stations are used interchangeably | Two stations work at the same time | Three stations work at the same time | Stations are used interchangeably | Two stations work at the same time | Three stations work at the same time | |
Random accessory | Punching die: 8 sets | φ7、φ9、φ11、φ13、φ17、φ21、φ11×15、φ13×17 | |||||
Shearing die: 1set | 160 | ||||||
Bending die:4 sets | Large flat bending, small flat bending、Super vertical bending 、U-sharped bending | ||||||
Embossing die | 130×40 | ||||||
Customized die | Common four-hole die | φ17×60、φ13×50、φ11×40、φ9×30(others can be made as the request ) |
303 Turret Type CNC Busbar Processing Machine
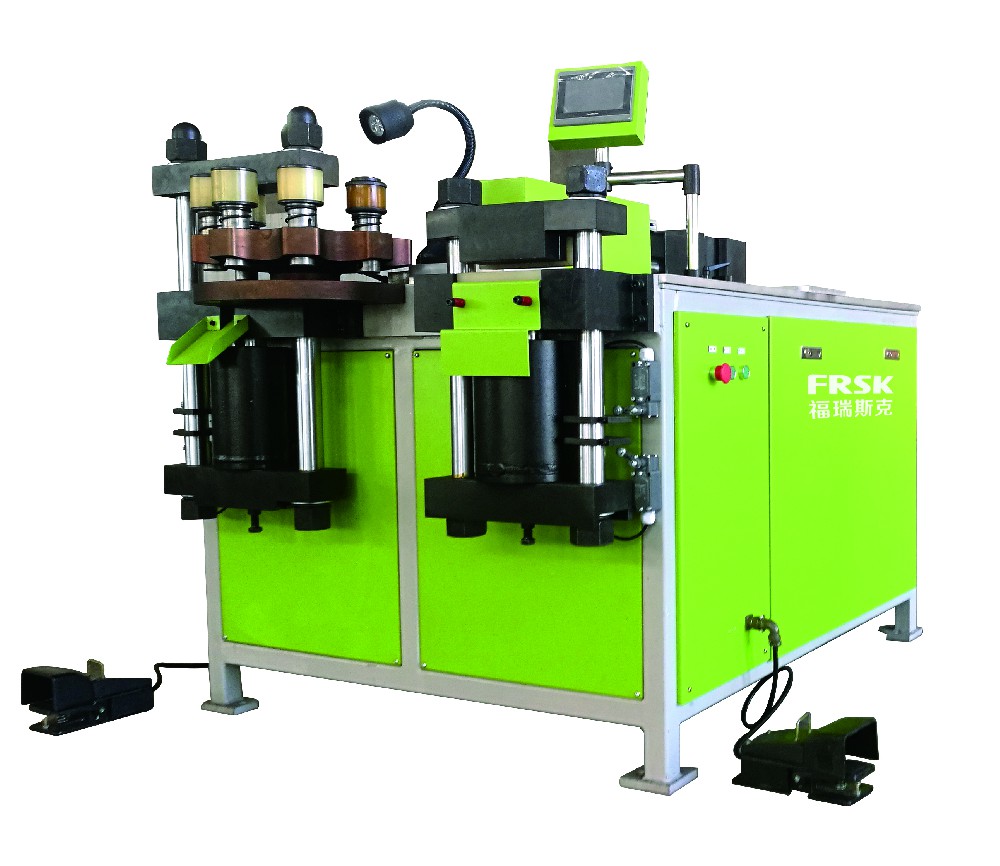
Application Area
This machine is mainly used to process various specificaitions of copper .aluminum busbars, Users can punch / shear / fold the busbars as long as they choose the corresponding processing unit,high efficiency ,it is the ideal machine for high and low pressure electric appliance manufacturing industry .
Technical Features
Plum blossom turret eight mode ,turret part is made of ductile iron(service life of single hole improves 3 times ,whole service life improves more than 20 times ),long holes.round holes can be arbitrary mixed ;large tonnage oil cylinder is used for shearing , shearing workpiece double section is vertical; the standby pressure of oil pump decreases,service life improve several times .
Model/Specificaiton | 303ZT | 303ZT-2 | 303ZT-3 | 303ZT | 303ZT-2 | 303ZT-3 | |
303ZTSK | 303ZTSK-2 | 303ZTSK-3 | 303ZTSK | 303ZTSK-2 | 303ZTSK-3 | ||
Number of punching mode | Punch eight mode | ||||||
Punching process | Max.punching force(KN) | 300 | 300 | 300 | 300 | 300 | 300 |
Punching range(mm) | φ4.3~φ25 | φ4.3~φ25 | φ4.3~φ25 | φ4.3~φ25 | φ4.3~φ25 | φ4.3~φ25 | |
Max.processing thickness(mm) | 16 | 16 | 16 | 16 | 16 | 16 | |
Max.processing width(mm) | 160 | 160 | 160 | 160 | 160 | 160 | |
Shearing process | Max.shearing force (KN) | 500 | 500 | 500 | 500 | 500 | 500 |
Max.shearing thickness(mm) | 16 | 16 | 16 | 16 | 16 | 16 | |
Max.shearing width(mm) | 160 | 160 | 160 | 160 | 160 | 160 | |
Bending process | Max.bending force(KN) | 300 | 300 | 300 | 300 | 300 | 300 |
Max.bending width(mm) | 160 | 160 | 160 | 160 | 160 | 160 | |
Max.bending thickness(mm) | 16 | 16 | 16 | 16 | 16 | 16 | |
Vertical bending process | Bending width(mm) | 30~120 | 30~120 | 30~120 | 30~120 | 30~120 | 30~120 |
U-sharped bending process | Bending range(mm) | >80 | >80 | >80 | >80 | >80 | >80 |
Worktable size(mm) | 1400×1200×900 | ||||||
Main motor power(KW) | 4 | 2×4 | 3×4 | 4 | 2×4 | 3×4 | |
Weight(T) | 1.2 | 1.3 | 1.45 | 1.2 | 1.3 | 1.45 | |
Instruction | Stations are used interchangeably | Two stations work at the same time | Three stations work at the same time | Stations are used interchangeably | Two stations work at the same time | Three stations work at the same time | |
Random accessory | Punching die :8 sets | φ7、φ9、φ11、φ13、φ17、φ21、φ11×15、φ13×17 | |||||
Shearing die :1 set | 160 | ||||||
Bending die :4 sets | Large flat bending, small flat bending、Super vertical bending 、U-sharped bending 1 set each , Embossing die(130*40) |